
После того, как торгующиеся на Мосбирже ПАО «Нижнекамскнефтехим» и ПАО «Казаньоргсинтез» вошли в состав ПАО «СИБУР», мы долго не видели от них годовых отчётов, красивых картинок и прочего. Потому мои обзоры технологий нефтехимии, которые я писал в этом бложике, с мая 2022 года были прерваны и я занялся чтением годовых отчётов российских публичных компаний. Недавно обнаружил, что теперь уже дочки СИБУРа имеют новые корпоративные сайты и даже годовые отчёты за 2022 год, и решил вернуться к рассказам о химической технологии.
Стоит сказать, что компании стали гораздо более закрытыми, в годовых отчётах операционной деятельности посвящены по паре страниц, продукты теперь вперемешку представлены на общем сайте СИБУРа, ну и вообще индивидуальность компаний постепенно теряется — всё интегрируется в производственные цепочки материнского холдинга. Зато появились нормальные фотки в фотобанке, а не те поделки свадебного фотографа, что мне приходилось показывать вам раньше, рассказывая про НКНХ.
Сегодня разберёмся как на НКНХ производится полипропилен.
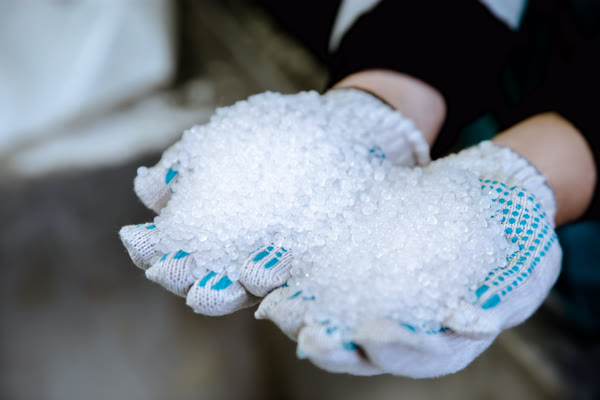
Гранулы полипропилена. Фото ПАО «СИБУР»
Полипропилен (ПП, или PP) — второй после полиэтилена по тоннажу мирового производства полимерный продукт с долей на рынке в 26%. По сравнению с полиэтиленом он имеет меньшую плотность, а значит — более легок. Вообще, полипропилен — самый легкий из массовых термопластов. Термопласты — полимерные материалы, способные обратимо переходить при нагревании в высокоэластичное либо вязкотекучее состояние.
Кроме того, полипропилен также более устойчив термически: эксплуатационные характеристики изделий сохраняются вплоть до 140—150 °С. Правда, полипропилен менее стоек к морозу, нежели полиэтилен: при отрицательных температурах он становится хрупким, поэтому использовать под нагрузкой изделия и детали из полипропилена в регионах с суровым климатом нельзя. Тем не менее из полипропилена изготавливают множество самых разных изделий, начиная от упаковочных пленок и заканчивая бамперами и приборными панелями автомобилей. Высокая кристалличность полипропилена (а хрупкость — ее обратная сторона) оказывается полезной при производстве из него прочных волокон и нитей.
Мономерное звено молекулы ПП состоит из трех атомов углерода и шести атомов водорода:

Структурная единица ПП
Из-за наличия метильной группы CH3, «торчащей» из цепочки, полипропилен чувствителен к свету и кислороду. Для снижения этого влияния в полипропилен вводят специальные вещества, называемые стабилизаторами, — они тормозят деструктивные процессы в полимере.
Наличие «торчащего» атома углерода влечет и другие весьма важные последствия. Оказывается, что характеристики полипропилена существенно зависят от того, как звенья ориентируются по отношению друг к другу:

Структура, в которой расположение боковых атомов носит хаотический характер, носит название атактической (А). Цепочка, где все боковые атомы углерода находятся по одну сторону, носит название изотактической (B). Если боковые углероды строго чередуются, то цепочка называется синдиотактической ©. Увеличение тактичности (регулярности расположения метильной группы) приводит к росту степени кристалличности, температуры плавления, прочности при растяжении, жесткости и твердости.
Достоверно неизвестно, когда впервые была осуществлена полимеризация пропилена. Однако до 50-х годов прошлого века полипропилен, в отличие от полиэтилена, не находил широкого применения. За предшествующие десятилетия наука довольно хорошо разобралась в закономерностях реакций полимеризации, стало ясно, как на процесс влияют температура и давление, а также характер среды, в которой идет реакция, были найдены и внедрены в промышленность высокоэффективные инициаторы полимеризации. Однако сама реакция, то есть присоединение отдельных звеньев к растущей цепи, не поддавалась, в сущности, контролю. Поэтому те полимеры пропилена, которые удавалось получать, сильно различались по своим свойствам — получались атактические низкомолекулярные (с малым числом звеньев в цепи) структуры. Характеристики таких полимеров не позволяли широко их использовать. Это и обусловило некоторое забвение полипропилена в первой половине XX века.
В начале 50-х годов ученые впервые попробовали использовать в реакциях полимеризации катализаторы, которые смогли косвенно управлять строением получающихся продуктов. Первые удачные опыты были выполнены, правда, с синтетическими каучуками. В 1952 году Карл Циглер поставил успешные эксперименты с применением нового типа катализаторов при синтезе полиэтилена. Его успехи способствовали активному изучению роли металлоорганических катализаторов при полимеризации. В 1953 году группа ученых из Миланского политехнического института под руководством профессора Джулио Натта модифицировала каталитические системы Циглера и провела опыты по полимеризации различных олефинов, в частности, пропилена. Полученное ими вещество коренным образом отличалось от всего того, что удавалось получить раньше: оно имело больший молекулярный вес (длину цепочек), было способно кристаллизоваться, имело более четкий температурный диапазон плавления, большую плотность и меньше растворялось в растворителях. Исследование структуры показало, что этот полипропилен имел линейную структуру и регулярность строения — то есть был изотактическим или синдиотактическим. За эти открытия Циглер и Натта в 1963 году получили Нобелевскую премию по химии, а примененные ими стереоспецифические катализаторы полимеризации с тех пор называются катализаторами Циглера-Натта.

Полипропиленовая упаковка, позволяющая дольше сохранять овощи свежими в среде инертного азота, стала экономически выгодной только после изобретения катализаторов Циглера-Натта
Первый изотактический полипропилен начали производить для продажи в Италии в 1956 году. Сначала на нефтехимическом заводе компании Montekatini в городе Феррара работала полуэкспериментальная установка, но в 1957 году там ввели в строй крупное по тем временам производство в 5 тыс. тонн/год. В 1959 году на этом заводе было освоено производство волокон из полипропилена.
Со временем выпуск полипропилена начался еще в ряде городов Италии, в 1962 году стартовало производство в США. В СССР производство полипропилена началось в 1965 году на Московском НПЗ (сейчас НПП «Нефтехимия» принадлежит совместно СИБУРу и «Газпром нефти»), где была применена отечественная технология. В 1977 году в Гурьеве (ныне Атырау, Казахстан) заработал завод, выпускающий полипропилен по итальянской технологии. В 1982 году производство полипропилена было пущено на нефтехимическом комплексе в Томске (сейчас принадлежит СИБУРу).

Томскнефтехим. Строительство установки по производству полипропилена, 1982
Для производства полипропилена используется, как правило, сырье трех видов: это пропилен пиролиза, пропилен из газов каталитического крекинга и пропилен, полученный дегидрированием индивидуального пропана. Стоит заметить, что более 90% себестоимости полипропилена составляет именно сырье – пропилен. В структуре производства 57% приходится на пиролиз, 23% – на вторичные процессы переработки нефти, 20% – на дегидрирование.
В России применяется три различных технологии получения полипропилена: Unipol PP, Innovene PP, Spheripol. На НКНХ применяют Spheripol, она является самой популярной в России (4 установки) и в мире, но уступает по тоннажу российским установкам на технологии Innovene PP.
Spheripol-процесс разработан компанией LyondellBasell (Нидерланды) и является модульной технологией, совмещающей жидкофазную полимеризацию в растворе мономера и газофазный процесс, состоящий из четырех основных узлов:
— подача катализатора;
— полимеризация в жидкой фазе;
— полимеризация в газовой фазе;
— узел отпарки полимерной массы.

Схема комбинированной установки по производству полипропилена Spheripol
Условия процесса: давление 15–33 бар (1 бар приблизительно равен атмосферному давлению), 65 °C, катализатор состоит из высокоактивного TiCl4, донора электронов, MgCl2 в качестве носителя и триэтилалюминия Al(C2H5)3.
В этом промышленном методе используется трубчатые петлевые реакторы, представляющий собой реактор типа «труба в трубе», большой высоты и относительно небольшого объема, заполненные жидким пропиленом, куда непрерывно подают катализатор. Производство различных марок полипропилена требует сополимеризации, например с этиленом, которая осуществляется в газофазном реакторе, куда переносится полимер из петлевого реактора. Пока в полипропилене нет никаких других мономеров, кроме пропилена, его называют гомополимером (ха-ха). Если нужна марка гомополимера — газофазный реактор просто обходится по байпасной линии. По сравнению с полностью газофазной технологией технологическая установка Spheripol предлагает на одной технологической линии полимеризации самый широкий спектр сополимеров, охватывающих все области применения полипропилена.

Слева в кадре петлевые реакторы производства полипропилена на СИБУР ЗапСибНефтехим. Фото ПАО «СИБУР»
Реакция полимеризации проходит с выделением тепла, тепло реакции удаляется с помощью охлаждающей воды, циркулирующей в рубашках петлевого реактора. Петлевой реактор используется потому, что он предлагает низкую стоимость и высокую теплопередачу, а также поддерживает однородную температуру, давление и распределение катализатора.

Вот эта балда — газофазный реактор. Фото ПАО «СИБУР»
Газофазный реактор представляет собой крупный цилиндрический аппарат с плавным расширением в верхней части, имеющей грушеобразную форму. В нижней части реактора расположена распределительная решетка с множеством отверстий. Ее основная задача — обеспечивать равномерное распределение циркулирующего реакционного газа по всему сечению реактора. Помимо этилена и со-мономеров в реактор вводится также водород. Он выступает регулятором молекулярной массы: его большая или меньшая концентрация в системе ведет к более ранней или более поздней гибели растущих полимерных цепей.
Полимеризация происходит в «кипящем слое» порошка готового продукта. Когда частицы набирают достаточную массу, они больше не могут поддерживаться током идущего вверх газа и спускаются в нижнюю часть реактора, откуда выгружаются. Реакционный газ-носитель теряет скорость в расширяющейся части аппарата, за счёт чего мелкие частицы полимера не уносятся через верхний штуцер реактора, а продолжают болтаться в кипящем слое, набирая массу. Реакционный газ-носитель рециклируется в нижнюю часть реактора.
Полученный полимер непрерывно выгружают из газофазного реактора в емкость для дегазации. Непрореагировавший пропилен отдувается в виде газа, очищается на фильтрах, охлаждается и конденсируется, после чего насосами возвращается в начало процесса. Отделенный порошок после фильтров попадает в отпариватель, где под действием водяного пара осуществляется деактивация катализатора и удаление остатков растворенных в полимере газов. После отпаривателя полимер попадает в сушилку, где в токе горячего азота осушается от влаги и остатков углеводородов. Воздух использовать здесь нельзя, так как горячий полипропилен неустойчив к кислороду воздуха и окисляется, теряя свои свойства.
Полученный продукт — порошок полипропилена — еще не является товарным. Для того чтобы он был готов отправиться к потребителю, в полипропилен необходимо ввести ряд добавок, а также превратить его в привычные круглые гранулы. Поэтому порошок отправляется на установку гранулирования.
Из бункеров хранения порошок отправляется на экструдер, где при нагревании превращается в расплав. В этот расплав вводят требуемые спецификациями определенных марок добавки — антиоксиданты, светостабилизаторы, термостабилизаторы, красители, антациды, осветлители и т. п. Комбинация и дозировка этих веществ может различаться в зависимости от производимой в данный момент марки полипропилена. После введения добавок расплав экструдером продавливается через узкое отверстие — фильеру, из которой выходит в виде тонкой нити, процесс экструдирования напоминает продавливание фарша через мясорубку.

Экструдер для грануляции полимера. Виден огромный электродвигатель и подходящая сверху гибкая труба для транспорта порошка. Фото ПАО «СИБУР»
Нить погружается в воду, охлаждается и ножами режется на гранулы. Потоком воды гранулы направляются на ступенчатую сушку, после чего поступают на так называемое вибросито — устройство, которое путем просеивания гранул через сито с определенным размером ячейки отбирает гранулы стандартного размера. Гранулы меньшего или большего диаметра удаляются и накапливаются в хранилище некондиционного материала.
Далее потоком воздуха (после введения стабилизаторов влияние на полипропилен воздуха и температуры уже не критично) стандартные гранулы направляются на гомогенизацию — необходимо добиться равномерных характеристик гранул в партии, поэтому весь продукт перемешивают. Гомогенизаторы представляют собой высокие цилиндрические бункеры, обычно смонтированные группой. При заполнении одного гомогенизатора начинает заполняться следующий, а первый перегружает полипропилен в товарные бункеры.

Силосы гомогенизации пропилена на СИБУР ЗапСибНефтехим. Фото ПАО «СИБУР»
Товарные бункеры имеют еще большую вместимость, чем гомогенизаторы, и способны накапливать крупные объемы. Из товарных бункеров полипропилен самотеком ссыпается на линию расфасовки, где автоматически взвешивается и упаковывается в мешки.

Мешки полипропилена. Фото ПАО «СИБУР»
Упакованный в мешки полипропилен размещается на складе, который, как правило, может осуществлять погрузку продукции как на автомобильный транспорт, так и в железнодорожные вагоны, для чего к складу проложена ж/д ветка.

Михалыч и киберпанк. Фото ПАО «СИБУР»
Теперь о цифрах. Производственная мощность ПАО «Нижнекамскнефтехим» по полипропилену составляет около 220 тыс. тонн/год. Это вторая по производительности установка в России, опережающая таких производителей как «Ставролен» г. Буденновск (Лукойл), «Томскнефтехим» (СИБУР), «Уфаоргсинтез» (Роснефть), «НПП «Нефтехимия» г. Москва и «Полиом» г. Омск (совместные СИБУР и «Газпром нефть») но уступающая «СИБУР Тобольск» с их 1 млн тонн/год.
В годовом отчёте 2022 Нижнекамскнефтехим обещает в скором времени задействовать для производства ПП пропилен с нового олефинового комплекса ЭП-600, а также хвастается, что в 2022 году достигли рекордной производительности по полипропилену, но конкретных цифр не называет.

Структура применения полипропилена в России
Всего в России производится около 2 млн. тонн/год полипропилена. За последние годы структура потребления полипропилена в России претерпела серьезные изменения: если раньше крупнейшим сегментом был пленочный, то сегодня он откатился на третье место, уступив товарам народного потребления (емкости, флаконы, тара, литьевые корпуса для техники и приборов, игрушки, предметы быта и обихода и т. п.) и пленочной нити. Вместе с тем полипропиленовые пленки играют весьма значимую роль на рынке гибкой упаковки. Главным образом речь идет о так называемых БОПП — биаксиально ориентированных полипропиленовых пленках. Их доля в общем объеме гибкой упаковки оценивается в 34% — это второе место после пленок из полиэтилена низкой плотности. В БОПП упаковывают практически все, в первую очередь продукты питания. Характеристики этих пленок делают их практически универсальными: они исключают прохождение воздуха и паров воды, инертны к большинству физических и химических воздействий, сохраняют эксплуатационные качества в широком диапазоне температур. Главными потребителями БОПП являются предприятия пищевой промышленности. В БОПП упаковываются хлебобулочные изделия, макаронные изделия, сахар, крупы, чипсы, хлопья, чай, кофе, майонез и т. п.
На российском рынке БОПП нефтехимическая компания СИБУР является ведущим игроком через свою дочернюю компанию «Биаксплен». Компания располагает несколькими линиями по производству пленок в Московской области, Курске, Самарской области, Нижегородской области и Томске общей мощностью порядка 180 тыс. тонн в год.
Мировые производственные мощности полипропилена составляют около 79 млн. тонн/год, но они загружены примерно на 90%. Крупными мировыми производителями полипропилена являются: LyondellBasell (Нидерланды) — крупнейший производитель с долей рынка около 11%, Sinopec (Китай), Sabic Saudi Basic Industries Corp. (Саудовская Аравия), PetroChina (Китай), Braskem (Бразилия).
Цена полипропилена на российском рынке сейчас находится в диапазоне от 156 тыс. руб/т до 176 тыс. руб/т в зависимости от марки. Если в 2022 году ПАО «Нижнекамскнефтехим» удалось реализовать 220 тыс. тонн полипропилена, то это принесло около 36,52 млрд. рублей выручки или 14% выручки от реализации продукции компании по РСБУ 2022.
/ (C) Источник
Не является индивидуальной инвестиционной рекомендацией | При копировании ссылка обязательна | Нашли ошибку - выделить и нажать Ctrl+Enter | Отправить жалобу