
Продолжаем изучать бизнес Нижнекамскнефтехима. Следующий продукт, который я хотел бы рассмотреть, это Изопреновый каучук. На Нижнекамскнефтехиме в получении изопренового каучука есть весьма интересная продуктовая цепочка, производство сырья для которой мы сегодня будем смотреть. Для этого вернёмся к компании «Газпром нефть» на Омский НПЗ и узнаем как получают нужную для нефтехимии бутан-бутиленовую фракцию (ББФ).
В прошлый раз мы рассматривали производство бензола из прямогонного бензина. Напомню, в результате атмосферной перегонки нефть разделяется на фракции, различаемые по температуре кипения: бензиновую, керосиновую, дизельную и прямогонный мазут. Из прямогонного бензина мы тогда сделали бензол, а вот остальные фракции отправили путешествовать дальше по установкам НПЗ. Посмотрим как там дела у одной из них — прямогонного мазута.
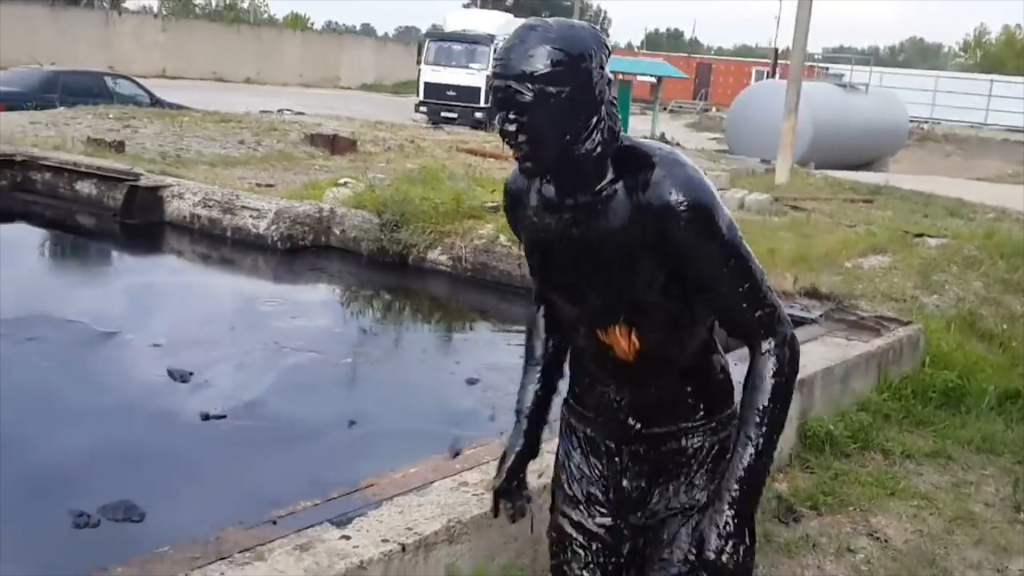
Дела у мазута нормально. Вопросов больше не имею
Прямогонный мазут – смесь углеводородов, кипящих выше 345-360 °С, направляют на разделение в вакуумную колонну. Мазут нельзя нагревать выше 360 °С — начнётся его термическое разложение, но разделить прямогонный мазут на фракции нужно. Для этого в вакуумной колонне при помощи эжекторов снижают давление до одной десятой атмосферного. Эжектор работает по принципу Вентури — если в канале жидкости или газа создать сужение, то за сужением образуется зона разрежения. В это разряжение и засасываются пары из ёмкости, где создают вакуум.

Как известно, снижение давления понижает температуру кипения жидкостей, а повышение – увеличивает (например, в скороварке). В вакуумной колонне углеводороды, имеющие от 26 до 60 атомов углерода в молекуле, которые не испарялись при температуре 360 °С в атмосферной колонне, начинают при этой температуре испаряться, а более тяжелые – все равно остаются жидкими. Таким образом можно разделить мазут без крекинга на фракцию, которая при атмосферном давлении испарилась бы в диапазоне температур 345–490 °С (если бы могла не разложиться, реальная температура в колонне ниже 360 °C) – она называется вакуумным газойлем, и фракцию, которая при атмосферном давлении начинала бы испаряться выше 490 °С и которая не кипит даже в вакуумной колонне — она называется вакуумным остатком или гудроном.

Мнемосхема узла вакуумной перегонки. Примерно с такими работают аппаратчики 6 разряда. Здесь отражены не все аппараты, а только те, показания приборов на которых, нужно контролировать на пульте. В центре — вакуумная колонна. Как видите, температура по колонне не превышает 338 °С, а на установке вакуумной перегонки этого завода получают 6 фракций
Вакуумный газойль при комнатной температуре представляет собой вязкую темно-коричневую непрозрачную жидкость, а гудрон – смолообразный твердый продукт черного цвета. Иногда в вакуумной колонне получают несколько вакуумных газойлей – например, для производства из них нефтяных масел разной вязкости. Но нас интересует лёгкий вакуумный газойль или маловязкий дистиллят (МВД). Его отправят на каталитический крекинг.

А вот так выглядит колонна вакуумной перегонки, которую мужики из Атоммаша (Волгодонск) сделали для Омского НПЗ. Длина 52 метра, диаметр 11 метров, масса 518 тонн. Почти как ракета «Протон М» (58 м). Когда такое оборудование проходит по Волге мимо Волгограда, некоторые думают, что ракету-то и везут. Логистика доставки была сложная, всего 12000 км: Волгодонск, Дон, Волго-Донской канал, Волга, Волго-Балтийский путь, вокруг Скандинавии, по Севморпути, Обь, Иртыш, Омск. Фото Росатом

Комплекс глубокой переработки мазута на Омском НПЗ. Фото «Газпром нефть»
Крекинг (англ. cracking, расщепление) — высокотемпературная переработка нефти и её фракций с целью получения, как правило, продуктов меньшей молекулярной массы. Крекинг протекает с разрывом связей С—С, то есть большие молекулы вакуумного газойля распадаются на молекулы поменьше.
Впервые каталитический крекинг был осуществлен в 1937 году в США, а уже в 1944 году в Советском Союзе в Грозном была запущена первая лицензионная промышленная установка каталитического крекинга.
Катализом в химии называют ускорение химических реакций (иногда и замедление, но его чаще называют ингибированием) под воздействием веществ (катализаторов), которые участвуют в реакции, но не входят в состав продуктов реакции. Катализаторы могут быть гомогенными (т.е. иметь то же фазовое состояние, что и продукты реакции, легко запомнить) или гетерогенными (т.е. иметь отличное от продуктов реакции фазовое состояние).
Промышленные установки каталитического крекинга – типичный пример гетерогенного катализа, поскольку катализаторы крекинга являются твердыми телами, а сырье и продукты реакции – жидкими или газообразными.
Катализаторы каталитического крекинга представляют собой микросферические гранулы с фракционным составом в пределах от 20 до 150 микрон. Средний размер гранул около 80 мкм. Катализаторы состоят из активного компонента – цеолита, кристаллического вещества с микропористой структурой, обеспечивающей основные реакции крекинга, и матрицы, основного вещества гранул, состоящего из алюмосиликата и оксида алюминия с пористой структурой.

Синтетический алюмосиликат кальция — цеолит
Процесс крекинга осуществляют на установках с непрерывно циркулирующим твердым катализатором, который последовательно проходит через зону реакции, а затем через зону регенерации самого катализатора. Необходимость регенерации катализатора вызвана тем, что в процессе крекинга поверхность катализатора быстро покрывается слоем кокса, препятствующего контакту катализатора и сырья. Этот кокс с поверхности катализатора выжигается за счет подачи в регенератор воздуха.
Поскольку вакуумный газойль, как правило, содержит большое количество серы, необходима его предварительная очистка перед проведением каталитического крекинга, иначе сернистые соединения будут негативно сказываться на катализаторе и качестве процесса.
Сырье подается в лифт-реактор на катализатор, поступающий сюда же из регенератора с температурой до 630 °С. На поверхности катализатора за короткое время происходит крекинг тяжелых углеводородов, за счет расширения вскипающих углеводородов катализатор движется вверх по реактору. Далее пары углеводородов поступают в ректификационную колонну на разделение продуктов, а катализатор под действием силы тяжести поступает в регенератор. Сюда подается воздух, кокс с поверхности катализатора выгорает и его активность восстанавливается. Катализатор за счет сгорания кокса вновь нагревается до 630 °С и поступает под действием силы тяжести в лифт-реактор. Общее количество катализатора, загруженного в установку, достигает 400 тонн.
Принципиальное отличие установок каталитического крекинга с лифт-реактором от других заключается в том, что катализатор никогда не меняют, а лишь понемногу добавляют в систему свежий катализатор.
Расход катализатора связан с тем, что в процессе постоянного движения с большой скоростью частицы катализатора соударяются между собой и о стенки аппаратов. В результате образуется катализаторная пыль, которая частично уносится с дымовыми газами из регенератора, а частично – с продуктами и оседает затем в составе шламов в товарных резервуарах. Регенерация катализатора и организация его беспрерывного движения внутри установки – наиболее сложные вопросы процесса каталитического крекинга.
Основные продукты каталитического крекинга.
1. Газовая фракция.
Газ каталитического крекинга наполовину состоит из непредельных углеводородов, в основном, пропилена и бутенов (бутиленов). Также присутствуют значительные количества изобутана. Благодаря этому бутан-бутиленовая фракция газа используется как сырье для производства различных полимеров и для процесса алкилирования с целью получения высокооктанового бензина. Эта самая бутан-бутиленовая фракция и нужна в нефтехимии. Её ещё иногда называют фракция С4, поскольку бутан и бутилен содержат по четыре атома углерода в молекуле. ББФ сжижают, фасуют в цистерны и направляют потребителям.
Пропан-пропиленовая фракция используется для выделения пропилена для производства полипропилена. Ввиду большой суммарной мощности установок каталитического крекинга, доля пропилена, вырабатываемого в процессе, составляет до 15% от его общего производства. Сухой газ (водород, метан, этан) используется в качестве топлива в печах заводских установок.
2. Бензин каталитического крекинга
В процессе каталитического крекинга вырабатывается высокооктановый бензин с октановым числом 88-91 пунктов. Кроме того, бензин содержит менее 1% бензола и 20-25% ароматических углеводородов, что дает возможность использовать его для приготовления бензинов согласно последним нормам Евросоюза (Евро-4, Евро-5). Основной недостаток бензина каталитического крекинга — высокое содержание непредельных углеводородов (до 30%) и серы (0,1-0,5%), что очень плохо влияет на стабильность топлива при хранении. Бензин быстро желтеет из-за полимеризации и окисления олефинов и потому не может применяться без смешения с другими бензиновыми фракциями.
3. Легкий газойль каталитического крекинга
Легким газойлем каталитического крекинга считается фракция продуктов с температурой кипения 200-270°С (реже 200-320 или 200-350). В ней содержится большое количество ароматических углеводородов, что приводит к низкому цетановому числу ( как правило, не выше 20-25). Кроме того, даже при условии предварительной гидроочистки сырья, в легком газойле содержится значительное количество сернистых соединений (0,1-0,5%). Из-за этого легкий газойль не может использоваться в больших количествах для приготовления дизельного топлива. Рекомендуемое его содержание в дизельном топливе — до 20% (в случае, если в топливе имеется запас по содержанию серы и цетановому числу). Другое применение легкого газойля — снижение вязкости котельных топлив, судовое топливо и производство сажи.
4. Тяжелый газойль каталитического крекинга
Тяжелый газойль каталитического крекинга — это фракция, начинающая кипеть выше 270°С (реже 320,350). Из-за большого содержания полициклических ароматических углеводородов эта фракция (при определенном содержании серы) является прекрасным сырьем процесса коксования с получением высококачественного игольчатого кокса. При невозможности утилизировать фракцию этим путём, её используют как компонент котельного топлива.

Производство катализаторов на Омском НПЗ. Фото «Газпром нефть»
За установками каталитического крекинга, безусловно, будущее нефтепереработки. Будут улучшаться катализаторы (в Омске для этой цели компания «Газпром нефть» организовала производство катализаторов), повышаться выходы и качество полезных продуктов. А если в дальнейшем установки каталитического крекинга будут в состоянии перерабатывать не только вакуумные газойли, но и прямогонные мазуты, углубление переработки нефти на этих установках может составить до 40%.

Михалыч исследует катализатор крекинга, чтобы было чем крякать вакуумный газойль. Фото «Газпром нефть»
Теперь о цифрах. Общая мощность установок каталитического крекинга в мире превышает 500 млн тонн/год по сырью. Омский НПЗ имеет две установки каталитического крекинга, суммарная производительность — 4,2 млн. тонн/год по сырью.
Омский НПЗ — крупнейший в России производитель бутан-бутиленовой фракции (ББФ) и занимает 25% общего объёма производства в стране. Другими крупными производителями ББФ в России являются «Лукойл-Нижегороднефтеоргсинтез» и Рязанская нефтеперерабатывающая компания («Роснефть»), вместе с Омским НПЗ на них приходится около 2/3 общего объема производства в стране. Входящие в «Роснефть» Ангарская нефтехимическая компания, Куйбышевский нефтеперерабатывающий завод и Сызранский нефтеперерабатывающий завод производят небольшие объемы ББФ — в сумме около 5% от совокупного российского производства (на 2015 г). ТАИФ-НК и входящие в «Башнефть» заводы помимо внутренней переработки поставляют продукт на «Нижнекамскнефтехим» и «Новойл» соответственно.
Крупнейшими потребителями ББФ являются нефтеперерабатывающие заводы, производящие алкилаты, а также предприятия нефтехимии, такие как Нижнекамскнефтехим, Омский каучук, Тольяттикаучук (Татнефть), Стерлитамакский НХЗ. Основные иностранные покупатели российской ББФ являются Польша и Белоруссия. Цена на ББФ в 2022 году составляет около 25000 руб/т.
/ (C) Источник
Не является индивидуальной инвестиционной рекомендацией
При копировании ссылка обязательна Нашли ошибку: выделить и нажать Ctrl+Enter