17 мая 2024 smart-lab.ru Бог Вычислений

Для этого надо вспомнить, что ПАО «Газпром» помимо своих газовых труб владеет химическим предприятием ООО «Газпром нефтехим Салават», в составе которого есть завод «Мономер», как раз и выпускающий 2-этилгексанол.
2-этилгексанол — органическое соединение, относящееся к классу спиртов. После низших спиртов (С1—С4) имеет наибольшее промышленное значение. С 1930-х годов используется преимущественно как спиртовой компонент при изготовлении пластификаторов для поливинилхлорида, а также при синтезе антиоксидантов для переработки эластомеров (каучука). В Салавате установка по производству этилгексанола была запущена в 1999 году.
2-этилгексанол в компании получают методом оксосинтеза нормального масляного альдегида с последующим гидрированием альдегидов и выделением 2-этилгексанольной фракции.
Вообще, производство 2-этилгексанола на ООО «Газпром нефтехим Салават» неразрывно связано с производством бутилового спирта, так как имеет с ним общие начальные стадии:
– получение синтез-газа;
– получение масляного альдегида.
Синтез-газ — смесь оксида углерода CO и водорода H2. Получают его углекислотной конверсией природного газа. Процесс во многом похож на кислородную конверсию метана, которую я описывал в статье о производстве метанола. Разница заключается в том, что вместо кислорода для конверсии используется углекислый газ. Использование углекислого газа позволяет получить в синтез-газе соотношение CO и H2 равное 1:1, тогда как кислородная конверсия даёт соотношение 1:2. Именно в соотношении 1:1 оксид углерода и водород будут вступать в реакцию получения масляного альдегида, так что очень удобно получить на стадии производства синтез-газа такое соотношение сразу, а не мучится с разделением CO и H2.
Второй этап — получение масляного альдегида CH3-(CH2)2-CH=O в процессе оксосинтеза. Оксосинтез, или гидроформилирование, — один из важнейших процессов современной химической индустрии. А открыл эту реакцию немецкий химик Отто Рёлен в 1937 году. Причем открыл случайно.
Рёлен работал сперва у Франца Фишера и Ганса Тропша в Институте Кайзера Вильгельма, а в 1934 г перешел в компанию Ruhr Chemie. Занимался он одним и тем же — изучал и совершенствовал реакцию получения углеводородов из СО и Н2, то что сейчас называют синтезом Фишера-Тропша.
Про синтез Фишера-Тропша уважаемые инвесторы могли слышать в связи с компанией GTL, торговавшейся на Мосбирже, и ныне благополучно пребывающей в коме. Типичная компания «Южных морей», обещавшая построить завод по технологии Фишера-Тропша и собиравшая денежки с наивных ребят на это дело.

Завод, конечно, никто никакой не построил. Но это уже совсем другая история
Основная причина того, что технология Фишера-Тропша, широко распространявшаяся по миру до 60-х гг, ныне никому не нужна — создание крупных нефтедобывающих мощностей в Аравии, Северном море, Западной Сибири, Нигерии и Аляске. Когда в мире столько замечательной нефти, зачем делать её искусственно из газа и угля?
Но вернёмся к Рёлену и оксосинтезу. Одной из проблем, которую решал Рёлен, было образование летучих олефин-парафиновых фракций, газойля. Поскольку процесс в то время оптимизировали под максимальный выход моторных топлив, от газойля требовалось избавиться. Предполагалось возвращать его в реактор, подмешивая к синтез-газу. Рёлен хотел выяснить, могут ли легкие олефины газойля встраиваться в растущие на поверхности катализатора углеводородные цепи. Если да, то это не только решило бы проблему, но и увеличило бы выход бензиновых и дизельных фракций. В других экспериментах к синтез-газу подмешивали аммиак, надеясь улучшить селективность синтеза.
Все лабораторные установки были смонтированы параллельно, причем отходящие газы собирались в единый коллектор, соединенный с вентиляцией. И вот как-то Рёлен обнаружил в этой трубе твердое белое вещество. Анализ показал, что это альдимин — продукт взаимодействия альдегида с аммиаком. Аммиак был в сырье, а вот откуда в продуктах взялся альдегид?
Дальше везение заканчивается и начинаются собственные заслуги Рёлена. Он легко мог бы вычистить трубу и забыть об инциденте, тем самым пройдя мимо открытия. Дело в том, что альдегиды и другие кислородсодержащие вещества в продуктах превращения синтез-газа не являлись чем-то из ряда вон выходящим. Однако в то время альдегиды в таких реакциях считались просто промежуточными соединениями.
Рёлен же задумался, отчего характерных для синтеза Фишера-Тропша тяжелых гомологов не было? Он предположил совершенно независимую реакцию олефинов с синтез-газом и поставил специальные эксперименты.
Он совершенно правильно рассудил, что выход альдегида можно увеличить, подняв давление. Первые опыты в конце 1937 г были проведены под давлением 100 атм и температуре 243°С. Дальше стало понятно, что давление надо еще повышать, а температуру снижать. В итоге Рёлен далеко ушел от условий Фишера-Тропша и получил высокий выход альдегидов.
Любопытно, что начальство, по воспоминаниям Рёлена, поначалу негативно относилось к его опытам по гидроформилированию, заставляя его заниматься усовершенствованием синтеза углеводородов в соответствии с контрактом. Однако Рёлен, как и многие немецкие учёные, был тем ещё раздолбаем.
В сентябре 1938 г. была подана заявка на изобретение метода синтеза кислородсодержащих продуктов из олефинов и синтез-газа. Патенты были получены во Франции, Италии и даже США. Причем американский патент вышел в 1943 году, когда страны уже находились в состоянии войны. Немецкий же патент был получен только в 1952. Нелишне отметить, что после капитуляции Германии ее интеллектуальная собственность проходила по разряду трофеев, так что роялти Рёлен и Ruhr Chemie получали впоследствии только с немецких предприятий. Остальной мир пользовался открытием бесплатно, ибо нефиг тут мировые войны устраивать. Первую установку по производству спиртов и кислот по методу Рёлена на 10 тыс. тонн в год начали проектировать в феврале 1941 г. Завод в Оберхаузене был построен, но продукции до конца войны так и не дал.
Сначала катализатором гидроформилирования служили соединения кобальта. Реакция осуществлялась при 120-180°С и 150-300 атм. В 1960-х годах было установлено, что родиевые катализаторы аналогичного строения при гидроформилировании в 100-10000 раз более каталитически активны. Переход на родиевые катализаторы позволил снизить давления, необходимые для осуществления реакции, до 1-30 атм, а температуры — до 20-120°С; увеличился выход альдегидов с прямой цепью, упростилась технология рецикла катализатора.
Для получения масляного альдегида оксосинтезом гидроформилированию подвергается пропилен:
CH3-CH=CH2 + CO + H2 → CH3-(CH2)2-CH=O
Пропилен получают здесь же, в Салавате, в процессе пиролиза, про который можно почитать в моей статье.
Полученный масляный альдегид используют для получения бутилового спирта и для получения 2-этилгексанола. Нас интересует как раз второй вариант. Синтез 2-этилгексанола из масляного альдегида состоит из двух стадий:
– альдольной конденсации масляного альдегида с образованием 2-этилгексеналя;
– гидрирования 2-этилгексеналя в 2-этилгексанол.
Процесс конденсации нормального масляного альдегида в 2-этилгексеналь осуществляется в альдокротонизаторе при температуре 120–150 ºС и давлении 4-7 атм. в присутствии катализатора – раствора натра едкого. Данная смесь на выходе из реактора поступает в отстойник, где разделяется на органический слой – 2-этилгексеналь и водный слой, содержащий щелочь и соли натрия. После разделения в органический слой для лучшего удаления щелочи дополнительно подается вода и повторно отстаивается. Очищенный от щелочи 2-этилгексеналь поступает на стадию гидрирования. Отработанная щелочь и промывные воды поступают на утилизацию.
2-этилгексеналь подогревается паром в кожухотрубчатом теплообменнике, смешивается с потоком водорода и подается в трубное пространство реактора. Гидрирование 2-этилгексеналя осуществляется на катализаторе, которым заполнены трубки реактора. После реакторов гидрирования продукт – 2-этилгексанол – поступает в сепаратор, где удаляется газовая фаза, поступает на очищение от примесей и непрореагировавших продуктов. Далее 2-этилгексанол поступает на дополнительное гидрирование. После реактора товарный 2-этилгексанол откачивается потребителю.
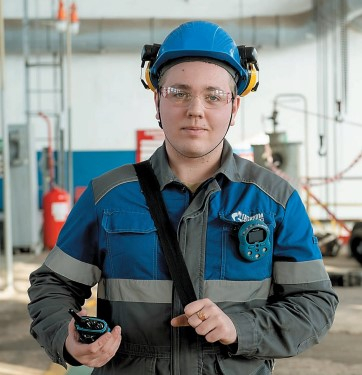
Михалыч и его трудовые будни: «Я устроился в Газпром, в „голубые каски“. Фото ПАО „Газпром“
Теперь о цифрах. Проектная мощность установки 2-этилгексанола на ООО «Газпром нефтехим Салават» – 34 тыс. тонн/год. В 2000 году проведена реконструкция узла гидрирования и ректификации. В 2020 году была проведена большая работа по перевооружению эстакады на установке гидрирования. Тогда же достигнутая мощность производства составила 37,6 тыс. тонн/год. В России 2-этилгексанол помимо ООО «Газпром нефтехим Салават» производят на предприятии Сибур-Химпром (г. Пермь), где производительность повыше — около 80 тыс. тонн/год.
2-Этилгексанол находит применение в качестве реагента для синтеза вторичных продуктов. Более 75 % этого вещества расходуется на синтез пластификаторов, 14 % — на получение 2-этилгексилакрилата, менее 10 % — на получение добавок к смазкам и маслам, менее 5 % — в синтезе поверхностно-активных веществ и в других областях.
Эфиры 2-этилгексанола занимают около 35 % общего рынка пластификаторов. Наиболее распространённым является сложный эфир 2-этилгексанола и фталевой кислоты, часто называемый диоктилфталатом (DEHP, DOP). Менее распространены диоктиладипадипинат (DEHA, DOA), триоктилмеллитат и диоктилтерефталат (DOTP). С 2005 года в Европе, а с 2009 года в США запрещена продажа игрушек и других предметов для детей, содержащих DEHP, поэтому эта область применения 2-этилгексанола постепенно уменьшается.
Основные мировые игроки рынка 2-этилгексанола: BASF SE (Германия), Sinopec (Китай), Eastman Chemical Company (США), Formosa Plastics Corporation (Тайвань).
Объем мирового рынка 2-этилгексанола в 2022 году составил примерно 4,48 млн тонн/год. Средняя цена на продукт на мировом рынке составляет около 1200 $/т.
Таким образом, установка 2-этилгексанола генерирует для „Газпрома“ около 4,1 млрд руб./год выручки или 0,07% выручки 2023 года по РСБУ. Скорее всего несколько меньше, так как продукт продаётся в основном в России, где цены на него пониже.
Не является индивидуальной инвестиционной рекомендацией | При копировании ссылка обязательна | Нашли ошибку - выделить и нажать Ctrl+Enter | Жалоба